Knowledge Points: Bending And Forming Of Sheetmetal
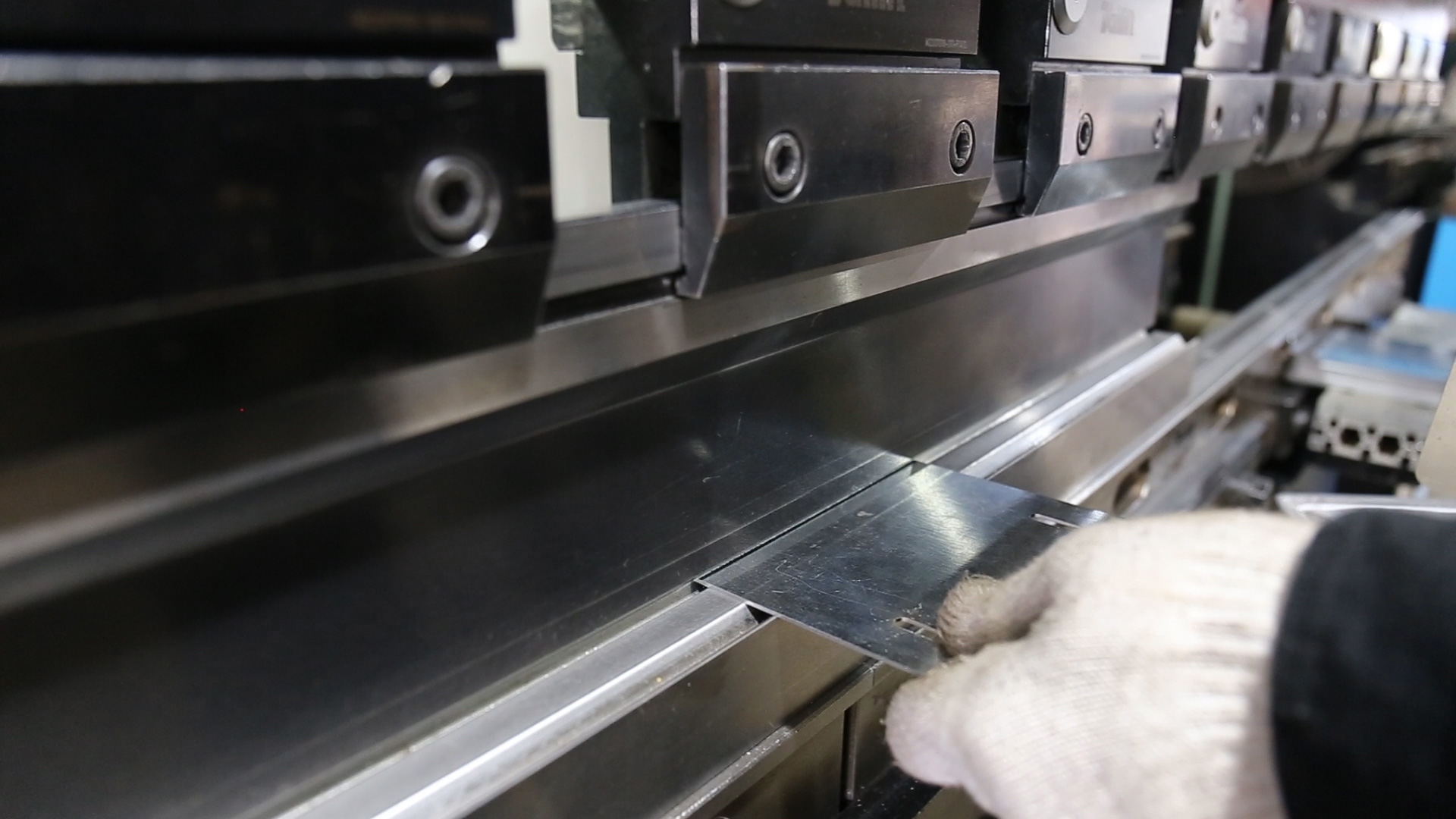
Knowledge Points: Bending And Forming Of Sheetmetal
Bending and forming of sheet metal is carried out on a plate bending machine. The plate to be formed is placed on the plate bending machine, the brake plate is lifted by a lifting lever and the workpiece is slid to the proper position, then the brake plate is lowered to the plate to be formed, and the bending and forming of the metal is achieved by applying a force to the bending lever on the plate bending machine.
Process Costs: Standard tooling costs (none), cost per part (low-moderate)
Typical products: consumer electronics, packaging, transportation and architectural metal parts, etc.
Output suitability: suitable for mass production (not more than 5000 pieces), can also be customized for single pieces
Quality: high bending accuracy with tolerances around 0.1mm (0.004in)
Speed: up to 6 bends per minute, although the initial configuration of the bending machine will take a longer time
Applicable materials: almost all metal materials, the most commonly used materials are: steel, aluminum, copper and titanium and other ductile metal plates
Design Considerations
1. Single piece bending length up to 16m (52ft)
2. The path of metal bending can only be a straight line.
3. The radius of the inner corner of the bend is one times the thickness of the sheet for ductile materials and three times the thickness of the sheet for hard materials.
4. If the sheet metal is not heat-treated, it can be bent up to 50mm (2in) thick.
The Process Is Explained In Detail (graphic + video)
The punch is driven by a hydraulic cylinder (providing vertical pressure) and the amount of pressure is determined by 4 factors: bending length, sheet thickness, ductility and bending radius.
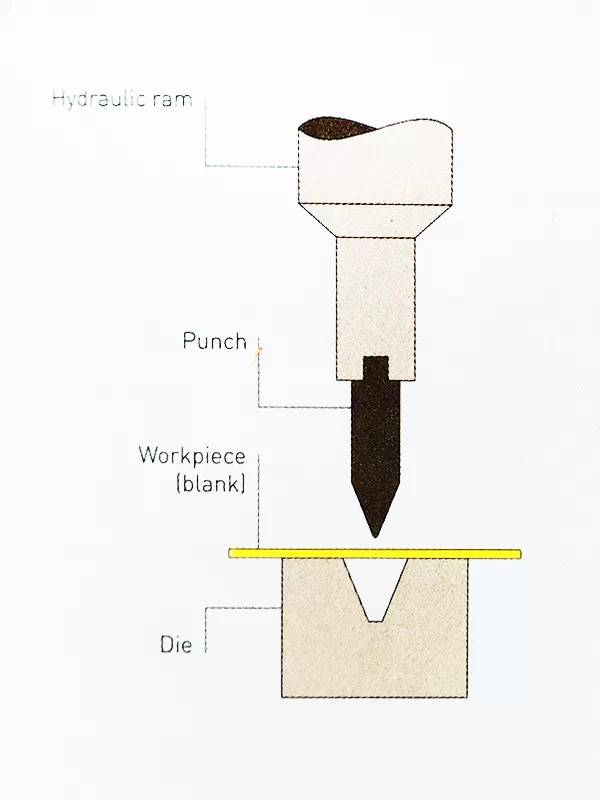
Step 1: Placement of the prepared sheet metal part on a rigid die
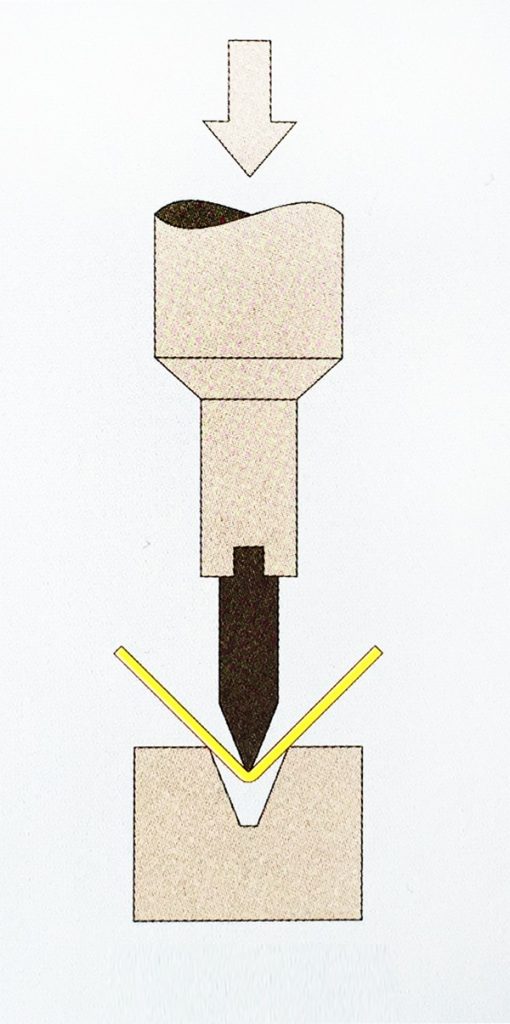
Step 2: The punch is driven by a hydraulic cylinder, which presses downward on the sheet metal part and bends it into shape. Each bending takes only a few seconds and the whole process is controlled by a computer.
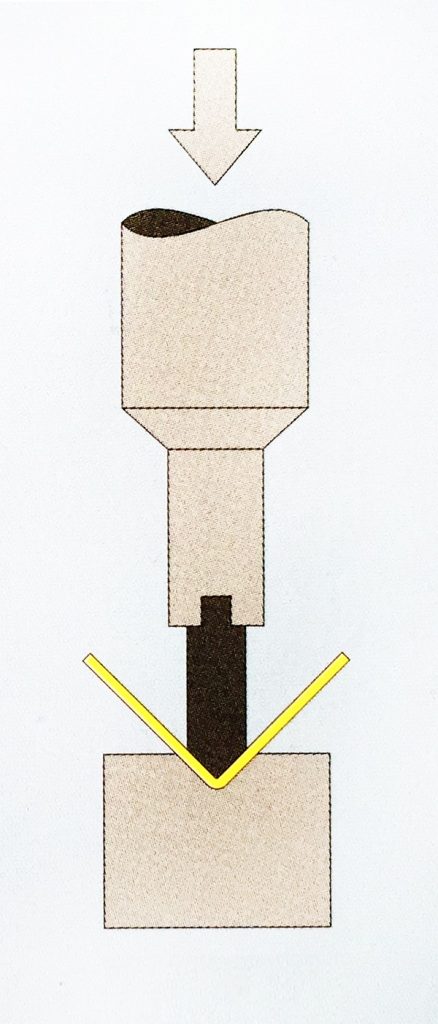
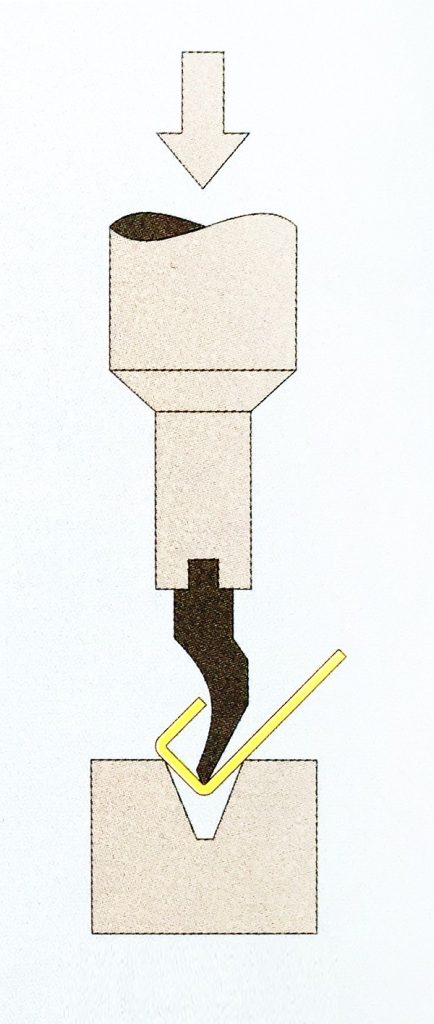
The shape of sheet metal bending is determined by the type of punch and the type of rigid mold, which is divided into standard and non-standard molds.